The Importance of Precise Injection Molding in Modern Manufacturing
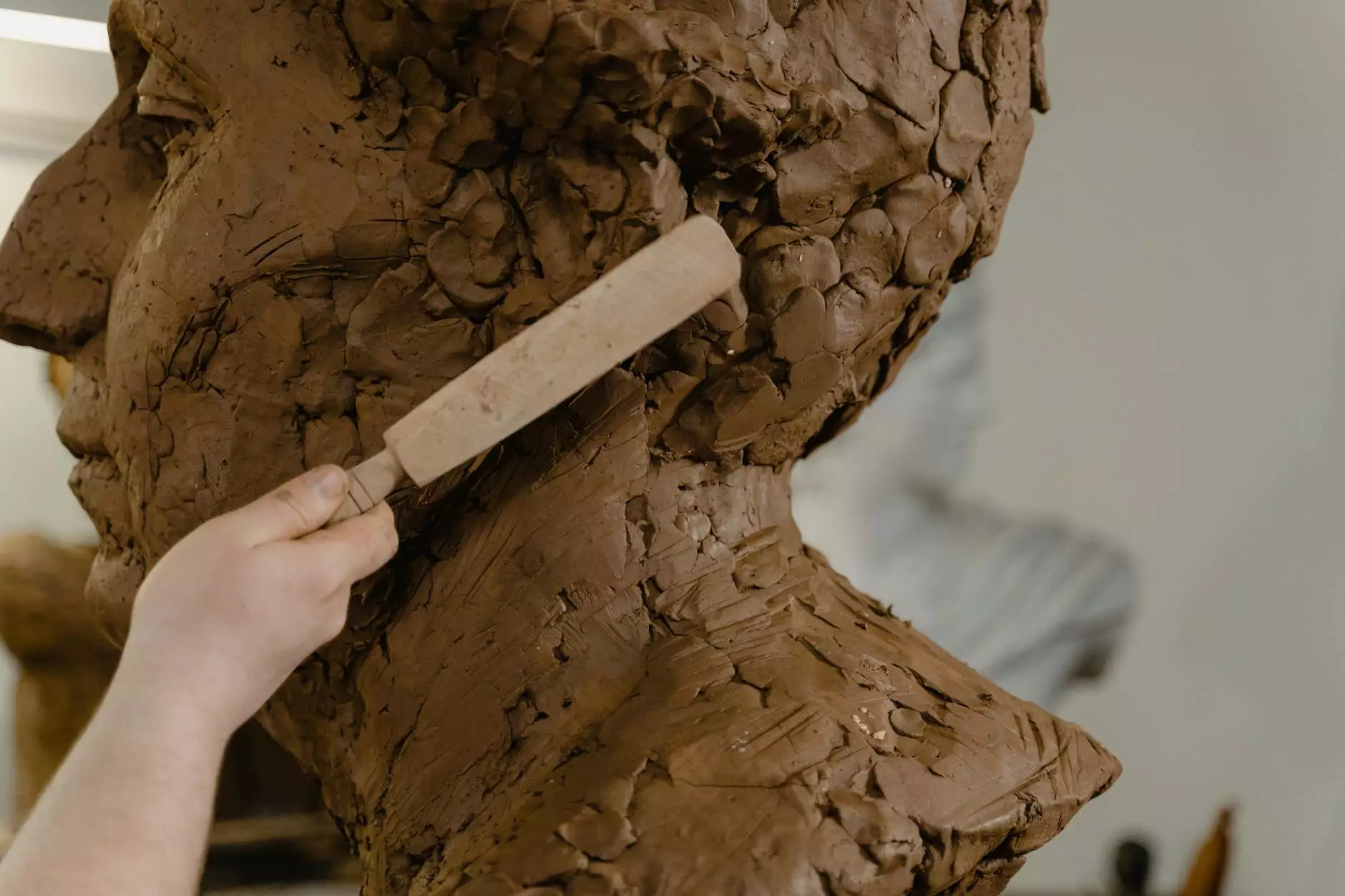
In today's rapidly evolving manufacturing landscape, the demand for precision and efficiency has never been greater. As businesses strive to deliver high-quality products while managing costs and production times, precise injection molding has emerged as a pivotal technique driving innovation and excellence in production processes. This article delves into the nuances of precise injection molding, examining its applications, advantages, and its significant impact on various industries.
Understanding Precise Injection Molding
Precise injection molding is a manufacturing process used to produce parts by injecting molten material into a mold. This technique is predominantly utilized with thermoplastics, where the material is heated until it becomes liquid and is then injected into specially designed molds to create specific shapes and forms. The process is known for its incredible accuracy and repeatability, which makes it suitable for high-volume production and applications requiring stringent tolerances.
The Process of Injection Molding
The injection molding process involves several critical steps:
- Material Selection: The right type of plastic or composite is chosen based on the requirements of the final product.
- Heating: The chosen material is heated in a barrel until it reaches its melting point.
- Injection: The molten material is injected into the mold at high pressure.
- Cooling: The material cools and solidifies within the mold, taking its shape.
- Demolding: Once the part has cooled sufficiently, the mold is opened and the part is removed.
Applications of Precise Injection Molding
Precise injection molding is utilized across various industries due to its versatility and efficiency. Here are some key applications:
- Automotive Industry: Used extensively for producing components such as dashboards, bumpers, and interior trim parts.
- Medical Devices: Essential for creating precise and sterile components like syringes, catheters, and surgical tools.
- Consumer Electronics: Employed for casings and internal components of devices like smartphones and laptops.
- Packaging: Critical in producing bottles, containers, and other packaging materials that must meet high safety and quality standards.
The Advantages of Precise Injection Molding
The use of precise injection molding brings numerous advantages to manufacturers:
- High Efficiency: Capable of producing thousands of identical parts in a fraction of the time compared to other methods.
- Cost-Effectiveness: The high initial cost of molds is offset by the low cost per unit when producing large quantities.
- Design Flexibility: Allows for intricate designs and modifications without significant changes in the manufacturing process.
- Material Versatility: Compatible with a wide range of materials, offering options like plastics, metals, and composites.
- Reduced Waste: The process is highly efficient, resulting in minimal waste of materials compared to traditional machining processes.
Challenges in Precise Injection Molding
While precise injection molding has many advantages, it is essential to acknowledge its challenges:
- Initial Cost: The cost for designing and creating molds can be significant, deterring small businesses from utilizing the process.
- Technical Complexity: Requires specialized knowledge and equipment to ensure precision and maintain quality controls.
- Material Limitations: Not all materials are suitable for injection molding; careful selection is necessary to achieve desired outcomes.
Quality Control in Injection Molding
Maintaining quality in precise injection molding is paramount for successful production. Incorporating quality control measures can help prevent defects and ensure consistency:
- Regular Mold Maintenance: Routine inspection and maintenance of molds are essential to maintain precision.
- Temperature Monitoring: Maintaining optimal temperature during injection and cooling can prevent material defects.
- Process Monitoring: Utilizing sensors to monitor the injection process allows for real-time adjustments to ensure precision.
- Material Testing: Conducting tests on raw materials prior to production can safeguard against defects in finished products.
The Future of Precise Injection Molding
The future of precise injection molding is poised for exciting advancements. With the rise of digital technologies and Industry 4.0, the integration of automation, artificial intelligence, and advanced diagnostics is transforming traditional manufacturing practices. Here are some anticipated trends:
- Smart Manufacturing: IoT-enabled machines that communicate with each other to optimize production efficiency.
- 3D Printing Integration: Combining injection molding with 3D printing for rapid prototyping and lower costs.
- Sustainability Initiatives: Development of eco-friendly materials and processes to minimize the environmental impact.
- Customization: Enhanced capabilities for producing customized parts on a large scale to meet consumer demands.
Conclusion
In conclusion, the role of precise injection molding in the manufacturing sector cannot be overstated. As industries continue to evolve, the need for precision, efficiency, and quality will drive the adoption and advancement of this technology. Understanding its processes, applications, and benefits will be crucial for businesses looking to thrive in competitive markets. Emphasizing quality control and staying abreast of technological advancements will ensure that companies maximize the advantages of precise injection molding in their production strategies.